How To Make Solder Tip
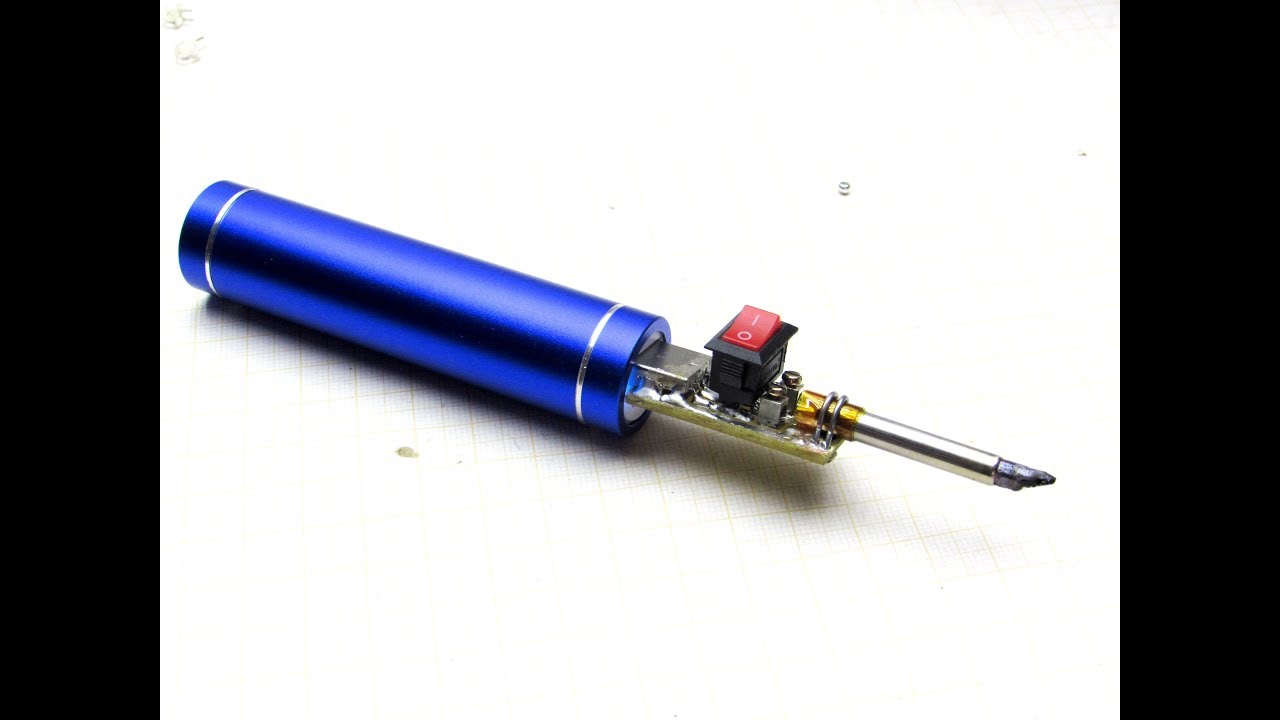
Begin by making sure the tip is attached to the iron and screwed tightly in place.
How to make solder tip. Place the soldering iron tip onto the sensor and apply solder as if you were making a solder connection. Dont be afraid to move your panel so that you get the best angle for running the bead. Here are nine soldering tips and mantras Ive gathered through the years that help me remember proper solder protocol.
Steel is not that good material for tips because it has very low thermal conductivity compared to copper. Start with a Clean Tip. Of solder under the tip.
We clean the soldering tip and we place the components one by one so I will solder this IC socket which has 16 pins. And the electric components size and shape finally select the one that you think or feel comfortable using. The soldering lead and the iron tip should be at an angle of 45 degrees so as the make the solder flow easily.
Apply very little flux in the solder joints and make the soldering. Keeping a soldering iron at a higher than needed temperature can damage the work product as well as shorten the life of the tip. Two things you should do to make them last long is turn the iron off whenever you dont need it and not use abrasives or wet sponge to clean the tip those brass shavings cleaners are best.
If youre in the wrong position it will make soldering smoothly more difficult. Remember that the flame from the torch doesnt melt the solderthe flame heats the metal and that heat causes the solder to flow where you want it. We want the solder to flow nicely all around both the pad and the lead to make a good connection.
You want solder to flow up a seam not just melt. Simply use a damp sponge or coiled wire ball to wipe the tip before soldering and after use. After narrowing down the tip shape and size considering the thermal capacity of the PWB.